Earthenware glazes: description and application
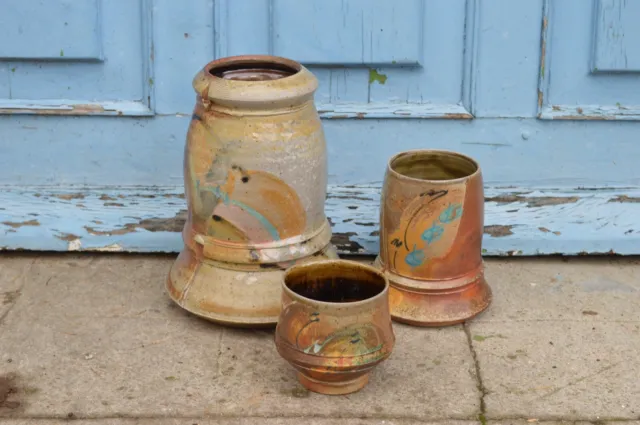
Summary
A little reminder about ceramic glazes
The special characteristics of low-temperature glazes
Frit formulas and glaze recipes
The particular case of tableware
As we saw in a previous article, a glaze is a melted glass that gives the ceramic piece both strength and protection. It also makes the surface waterproof and enhances colours.
Glazes applied to earthenware are different from stoneware glazes because they fire at lower temperatures. In France, the most common range is between 960°C (1760°F) and 1020°C (1868°F) for earthenware. In the UK, earthenware fires mainly around 1060°C (1940°F). You’ll need to check with your clay provider in your country to see at what temperature it’s best to fire your earthenware clay. But generally anything between 960°C (1760°F) and 1160°C (2120°F) is considered earthenware. Stoneware and porcelain, fire at a much higher temperature: in between 1240° and 1300°.
A little reminder about ceramic glaze
Glazes are essentially made up of silica.
Silica alone melts around 1700°C. Since this temperature is impossible to reach with a potter’s kiln (which does not exceed 1300°C), the melting point of this silica is lowered thanks to a physicochemical property called the “eutectic”: the combination of ingredients of 3 different pHs will lower the melting point of the glaze ( see our article).
How it’s done: we add to the silica (acidic pH) and alumina (neutral pH), an assembly of basic pH oxides, called:
- alkalis (mainly sodium and potassium) and
- alkaline earths, which are calcium, magnesium, strontium and barium
- we can also add zinc oxide.
Your choice of basic, acidic and neutral oxides will determine the characteristics of your glaze. The composition of the of the mixture of ingredients will influence its texture, as well as the appearance of the colours imparted by the colouring oxides, which are added at the final stage.
Mixing acidic, neutral and basic oxides will lower the melting temperature of a glaze to around 1245 °C (2273°F).
The special characteristics of low-temperature glazes
1245°C (2273°F) is still too high a temperature for earthenware glazes. This is why it is necessary to include more powerful fluxes in recipes for the low-temperature glazes we need for earthenware.
The two main powerful fluxes for lowering the melting temperature of glaze below 1000°C (1832°F) are: lead and boron.
Lead is toxic to the human body. It is still possible to use it in a glaze, as long as you protect yourself with gloves and a mask. It is mainly used to make decorative pieces; it should not be used for tableware, or any dish used as a food or drinking vessel, because lead causes lead poisoning or ‘plumbism’.
We will therefore focus more specifically on boron.
The American ceramicist Matt Katz has created a very interesting table to illustrate the amount in moles of boron one must add to a formula to lower the melting point:
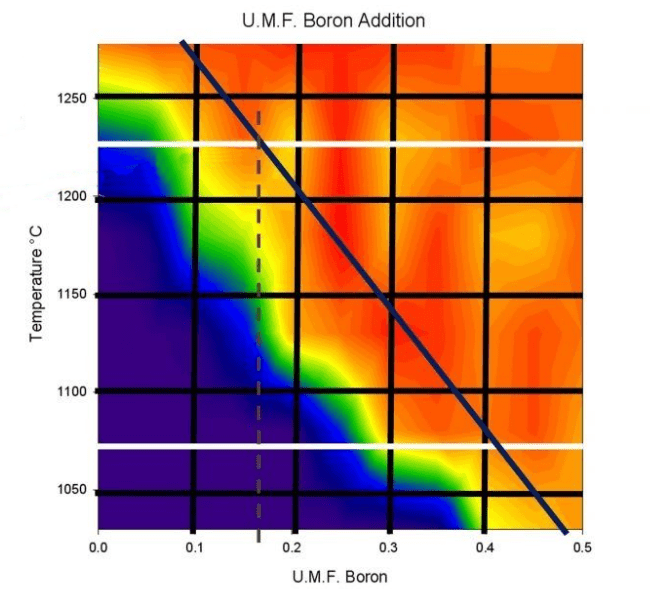
The black diagonal indicates the amount of boron in moles: for example, to lower a melting point from 1280°C (2336°F) to 1050°C (1922°F), 0.45 moles of boron must be added to the Seger formula. In our online course, we explain what a Seger formula is, how to use Matt Katz’s graph, how to use Glazy software to adapt any recipe from high temperature to low temperature.
Boron
Boron does not exist as such in nature, it exists in combination with other elements. The most common oxide, B2O3, soluble in water, is mixed naturally with other oxides such as calcium oxide (CaO) and/or sodium oxide (Na2O).
Boron compounds available from retailers are:
- Borax:(B2O3 +Na2O +10H2O) it is found in crystallized form (like powdered sugar) and requires a jar grinder.
- Colemanite : (B2O3 +CaO +5H2O): it is a finer powder than borax. However, the glaze can shrink or detach from the vessel.
- Gerstley borate (B2O3 +CaO +H2O) is preferable to Colemanite as it contains H2O, reducing the risk of glaze shrinkage or delamination (when the water evaporates during firing). It is not always stocked by French retailers. In the UK, some ceramicists substitute Gillespie borate (a proprietary formulation made by a US company), depending on the desired outcome.
- Ulexite (B2O3 +Na2O +CaO): this is the most practical product to use because, in addition to boron, the glaze contains sodium and calcium. It does not create any defects when the temperature rises.
The composition of these four products will vary from one dealer to another depending on where they were mined. Ceramicists who need to use a lot of boron in their glazes would prefer to use a chemically stable product instead; products that are not mined in a quarry but manufactured in a factory: these are called ceramic frits.
The ceramic frit
A frit is the result of an industrial process that allows boron to be incorporated into a glaze, making it more stable by bonding to silica.
To make a frit, the manufacturer heats the raw material powders in a crucible at a high temperature (without adding water). They combine in a vitreous mass – thanks to the eutectic process. The manufacturer then quenches the whole thing in water, creating a thermal shock which will” sinter” the glass into granules. The final step is to finely grind these granules to obtain the ready-to-use powder you will use in your glaze. This technique uses a much more powerful grinder than a jar grinder that a ceramicist may have in her or his studio.
Why use a frit?
The frit has two main uses:
- It makes it possible to incorporate products which would be soluble if they had not been fritted. These products include boron, sodium and potassium. If water-soluble compounds, such as boron, sodium or potassium, were used in a glaze, they would migrate first from the glaze solution into the clay when we apply the glaze, modifying the reaction when firing The clay would deform during firing, and the glaze would no longer have the elements necessary to melt, because the boron (or sodium or potassium) would be in the clay and no longer in the glaze. Sodium and potassium could be incorporated into the glaze through a feldspar. But for earthenware glazes, the feldspar would risk bringing too much alumina and too much silica (see the formulas of feldspars) which would not allow fusion at low temperatures.
- Frits make it possible to incorporate certain dangerous products when they are raw, such as barium: once fritted, it can be used without danger in the studio.
Frits in earthenware glazes
For the manufacture of earthenware glazes, we will therefore very often use a frit made from boron.
The frits on sale in France (Ceradel, Solargil, Como, Cousin etc.) melt at a specific temperature, between 700°C (1292°F) and 1100°C (2012°F), depending on their composition.
To make an earthenware glaze, we choose a frit that melts below 1000°C (1832°F). We then add silica and alumina to find the ideal melting point (like the Al2O3/SiO2 progression we use in our course on high-temperature glazes).
The frit will, to an extent, play the role of a feldspar in a high-temperature glaze: it will bring the basic pH ingredients. But, with a frit, the proportion of alumina and silica used will be much lower than in a high-temperature glaze made without frit. The latter already contains alumina and silica.
In our online course, we focus on making high-temperature glazes. There are 2 reasons for this:
- In some countries, like France, frits are expensive: you therefore don’t save much by making your own, you may as well buy them ready-made.
- Using a frit is not always easy… We explain why.
Frit formulas and glaze recipes
The frit is a complex product, made up of multiple ingredients.
Here is for example the composition of two frits, in moles. The first represents the simplest possible mixture (already including 5 ingredients!):
Frit FR 7 from the French manufacturer Solargil:
Na2O (Sodium) 0.60 mol
Al2O3 (Alumina) 0.22 mol
SiO2 (Silica) 2.74 mol
K2O (Potassium) 0.40 mol
B2O3 (Boron) 1.61 mol
The second is a formula for a slightly more complex frit:
Frit FR 6 from the French manufacturer Solargil:
SiO2 (Silica) 2.55 mol
Na2O (Sodium) 0.29 mol
B2O3 (Boron) 0.26 mol
Fe2O3 (Iron) 0.04 mol
Al2O3 (Alumina) 0.38 mol
K2O (Potassium) 0.19 mol
BaO (Barium) 0.05 mol
CaO (Whiting) 0.06 mol
PbO (Lead) 0.41 mol
In other words, a frit already looks like a glaze on its own.
If you find a glaze recipe that you like and you can easily get the frit used in the recipe (that may mean that the person who uses the recipe is in the same country as the suppliers of the frit), repeating this recipe will then be easy. Easier even than adapting a recipe without a frit because a particular frit always has an identical chemical formula – unlike feldspar, the chemical formula for which may vary between different quarries, or even between different parts of the same quarry.
But if your chosen recipe uses a frit that is not available in your country, then you will have to select another frit and adapt the recipe to the new frit’s chemical formula, as we explain in our online course.
Since frit recipes are complex, this makes it difficult to calculate the overall glaze recipe.
To do this, you will need to obtain the formula for the frit, its molecular weight, and its melting point. Suppliers will be able to provide you with this information.
You can easily find the details of frits sold in Europe via the site of a French potter: Philippe Moutereau, who kindly shares the list and the formulas of practically all the frits that can be found in Europe.
Site for frit formulas: http://pmoutereau.free.fr/frittes/frittes.html
The particular case of tableware
Unlike stoneware and porcelain, earthenware remains porous after firing. This means that it cannot be used to contain liquid unless it is covered with a waterproof glaze.
If you want to make tableware with earthenware, any crazing in the glaze will make it unsuitable – it will no longer be waterproof. On the other hand, if you won’t use your ceramics for tableware, crackling can be sought after as they bring very beautiful effects!
A glaze crazes when it does not have the same Coefficient of Thermal Expansion (CTE) as the clay onto which it is placed. Both clay and glaze expand during firing because the silica in both expands. If this momentary “expansion” is not the same for the clay and the glaze, if one expands more than the other, then the glaze will be forced to move over the vessel’s surface, causing crazing.
As this effect depends both on the clay and the glaze you use, reproducing a low-temperature recipe (which says it does not craze) from another ceramicist does not mean it will be the same for you: you won’t necessarily be using the same clay.
If you follow a recipe to make a glaze for earthenware tableware and don’t want crazing, even if you can get hold of the same frit as stipulated in the glaze recipe you are following, you will have to do some tests – as described above – to find a balance between the frit and the added alumina and silica. It takes experience and practice.
Crazing is not always visible. To check for its possible presence, put water in the pot and wait overnight to see if it leaks.
For your first attempts
If you are not looking to make tableware and you do not feel ready to calculate your glazes yet, you can make some simple first attempts as follows:
- Obtain a frit that melts below 1000°C (1832°F) from a retailer near you. Add alumina and silica little by little, either using a Kaolin (alumina+silica), or using a feldspar (alumina+silica+sodium+potassium) with slow progressions of 5 g by 5 g per 100 g of frit. You can add up to 25 g of kaolin or feldspar.
- You will go from a “runny transparent” glaze to matte/underfired white, with all the intermediate textures. Once you have chosen your texture, you can start another progression with colouring oxides.
The melting point and the colour of the glaze will be directly related to the clay you are using. Results can be very different from one clay to another.
This simplified technique does not, of course, always eliminate crazing in the glaze, and therefore the pot may not be waterproof – earthenware’s major drawback.
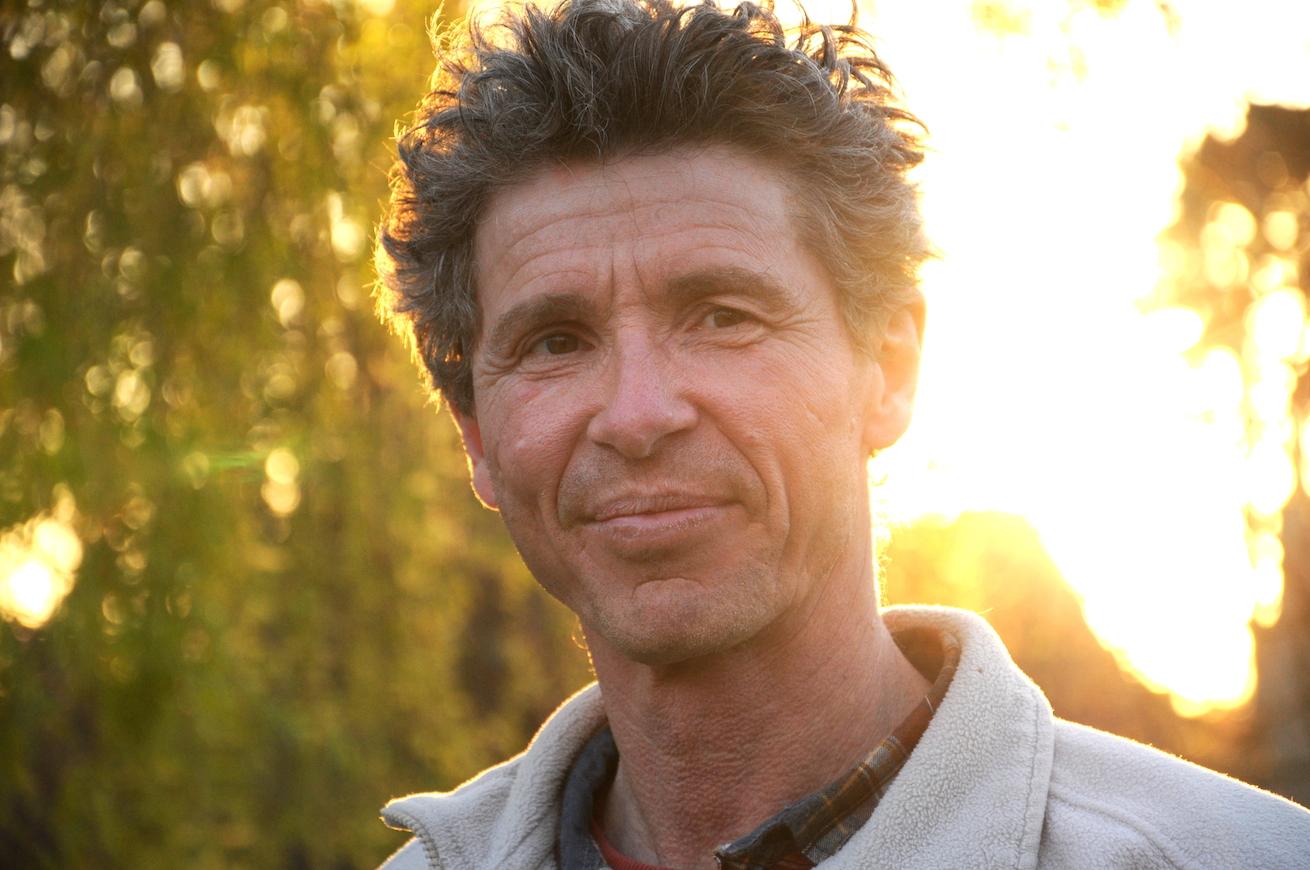
Resource centre
animated by Matthieu Liévois,
potter-ceramist for over 40 years and founder of the Creamik School
Find all the courses
Keywords
Don’t miss any more news from the Créamik school!