Matthieu Liévois, The search for crystals
Cristallisation with copper red, Matthieu Liévois
Every year, Creamik’s students present their work at an end of the year exhibition in June. True to the school’s tradition, they showcased their ceramic creations in Port Anna, on Ti-Anna’s roof. But this year, the tradition was enriched by new ideas: the students chose to exhibit collectively, thus highlighting their shared background and the technical subtleties they had acquired throughout the year. This approach enabled the public to appreciate the richness and complexity of their apprenticeship.
Another welcome innovation was this years’ invitation extended to a group of musicians, and the president of the local Sinagots association made available a sailboat for the exhibition. The festive atmosphere thus extended far beyond the world of pottery.
Among this year’s remarkable achievements were several crystalline glazes with particularly impressive aesthetic renderings. These exceptional achievements are an opportunity to highlight the techniques that have driven Matthieu throughout his career as a ceramicist.
We invite you to revisit our previous article, which will guide you through your first crystallization experiments: https://creamik.com/crystalline-glazes/?lang=en
Results from a student firing at Creamik School, june 2025
In the following interview, Matthieu explains how he explored and developed this technique. His investigative approach keeps the reader on the edge of their seat until they discover results as unexpected as they are remarkable.
Matthieu, can you tell us how you came to crystalline glazes?
It was pure chance. I met Lucette Pillet at a trade show at Porte de Versailles in Paris, who had worked as a potter for a long time, but in a glassworks where crystal was also blown. When I discovered her work, I asked her about it, as it was the first time I’d seen the phenomenon of crystallization. She was putting powdered crystal mixed with water on her porcelain after the first firing. I think she had trained in the United States, and must have met potters who practiced this kind of technique. She knew roughly what to put in her glaze. But she didn’t tell me in detail, of course!
She knew that impurities were needed in the crystal, what we call germs, for the crystals to form. So she had tried different products: tungsten, titanium, rutile… and she started to get crystals, but she didn’t really know that it was during cooling that the phenomenon appeared. She fired at around 1280°C-1300°C and let the kiln cool naturally.
I was very interested in all this work. I tried to document it, but at that time, in 1985, 40 years ago, there was nothing written, and nothing on the Internet. There was nothing… but I was a young potter!
What guided you at that time, in the absence of precise information?
At the time, I was living in Paris, in the 2nd arrondissement, next to Beaubourg, so I started looking in the Beaubourg library for a book on arts and crafts. And I came across an American book, which didn’t exist in French, in which there was a chapter on this crystalline glaze technique, but it didn’t give any recipes, it just gave some hints.
So I set about deciphering this famous chapter. Some time later, I left Paris and moved to the Charente region, where I began my quest for crystalline glaze, following the few clues I’d found. I had no idea what temperature to conform to or what I needed in addition to the crystal. I didn’t even have a crystal! So I started with glass powder, which was the closest I could get…
How did you get hold of the glass, and at what point did you feel you were beginning to understand something fundamental?
I used to collect glass bottles and crush them myself. I tried all sorts of things. What I didn’t know at all was that crystallization firing was an oxidation process.
But I was doing reduction! In fact, as the book I’d consulted was in English, I’d let a bit of information slip.
I understood that you needed very little alumina because the book said “Al2O3” and quite a lot of zinc oxide (ZnO); you needed Na2O, KNaO, little CaO; there could be other products like barium, magnesium… I understood the acronyms.
So I did some research, but I did it empirically. What’s more, at the start of my career, I wasn’t really used to doing molecular calculations. It was only much later that I realized the value of molecular calculations. I must have done 3,000 to 4,000 trials. And it never worked, even though I knew it could.
In my gas kiln, there was an oxidation firing. One day, I put a test tile in this oxidizing zone, and that’s when I saw the crystals appear – a miracle!
So, in the end, your major discovery was the role of cooling?
Yes, I understood a key piece of information about crystallization: you have to fire during oxidation. So I did a few more firings, and gradually I got the hang of it. At first, I had 1 or 2 crystals. But I still had no notion of cooling stages; I cooled in the conventional way.
At that time, I read an article on luster glazes, where they were smoke-fired at lower temperatures. So it occurred to me that, since smoke-firing was done at lower temperatures, why not work on “cool-firing” for crystallization too?
So I started to slow down the cooling, but I didn’t know exactly how. As I experimented, I decided that instead of cooling down slowly, I’d lower the temperature as usual and restart the kiln. So I restarted the kiln at 1250°C, at 1220°C and as I went down further, I reached 1100°C, and that’s when I saw that the crystals were the biggest.
Finally, I carried out some basic research, but it wasn’t just on the glaze recipe itself, I realized that I had to work on the firing as much as the glaze. And what was even more incredible, I had to work on cooling.
It’s true that in the ceramics school where I trained, we talked about firing curves, but once the kiln was finished, we turned it off, waited and did nothing more. But it’s precisely at this point that we need to take action again.
At the end of the day, this meant very long firing times, which could last 15h, 16h, 17h…
After these initial conclusive results, how did you simplify your research, having started by crushing glass by hand?
I thought that if Lucette Pillet had found her technique with glassmakers, why not go to their catalogs and look for glass powder? That’s how I stopped crushing glass, and saved a lot of time!
Then I started working with frit, because frit is glass powder. In ceramics, we used frits rather than glass powders.
What was your kiln at the time? Was it a determining factor in your approach?
I had a Scandia forced-air kiln, so I could easily obtain the atmosphere I wanted. It was the first kiln I had back in 1988, when I set up in Charente.
How were you received when you first exhibited your crystalline glaze pieces?
I remember the first potters’ market I ever did, in the Dordogne, at Bussières-Badil. I had 3 or 4 pots with crystalline galzes. A guy from Limoges stopped by and, looking at my crystals, said: “I’d heard about that, but I didn’t know it existed”, and he bought all my crystallized pieces. So that gave me strength, it boosted my desire to carry on! Because crystalline glazing were still quite new in France!
So I carried on, while developing my other production and research on stoneware. I found that crystalline glaze on stoneware was much less beautiful. So I developed crystallization on porcelain, but I also made a lot of stoneware tableware. So I had a stoneware production for my utilitarian production, with more classic glazes… and a personal research production on crystallization that I worked on when I was on vacation.
How did you go from pure crystallization to color?
I used coloring oxides as in a classic glaze. I also tested mixtures of oxides.
I also used lithium, as it allowed for certain colors. With oxides such as nickel, it gave blue crystals, whereas in classic stoneware glazes, nickel gives green or yellow colors. And here I had blue. So I incorporated lithium either with lithium oxide or with lithic feldspar.
Little ball vase, Nickel blue, Matthieu Liévois
And the red? How did you manage to make copper red when copper red is known to appear reduced?
Well, I kept on working, and one day I made a blunder, a blissful blunder with my forced-air kiln! The big advantage of the forced-air kiln is that you control the air you put into the kiln. The air comes in through one pipe, and the gas comes in through another. So we can regulate the quantity of air and the quantity of gas very precisely, to the nearest gram of air and the nearest gram of gas. That’s what makes it possible to always have the same atmosphere, and to reproduce it.
And one day, when I was tired, I made my usual stops at around 1100°C to start the crystals. Moreover, I had noticed that when I did a little smoldering at around 1000°C, I could make my glazes satin to matte, which, without this smoldering, came out very shiny. So I knew that glazes could be matted by an excess of gas, and so I left a little gas and a little air to cool down to around 800°C. The atmosphere became reducing, but it didn’t change the color of the glazes.
And one day at 800°C, to stop the kiln, I wanted to turn off both the gas and the air, but I did the opposite! I did shut off the air, but I had turned the gas all the way up, so I didn’t realize it right away. Suddenly, a huge black smoke filled my studio. And after 3 minutes, I smelled gas and rushed to turn off the gas. So I’d done a really big smoke job, there was nothing left but gas and no air at all, it was carbon monoxide, I could have poisoned myself… Frankly, I thought the production of this firing was ruined. The next day, when I opened the oven, the crystals, which were supposed to be green, came out red!
Unintentionally, I had reproduced the luster technique without altering the crystals.
Copper contains copper salts and copper oxides, and the salts rise to the surface during firing. So I reduced the copper salts, which were no longer oxides. So, the copper that usually gave me green crystals, well, when there’s a lot of gas and very little air, thanks to the smoldering process around 800°C, became copper red. If I’d done it at 1100°C, it wouldn’t have worked; here, it worked at a much lower temperature, like when smoke-firing a luster. .
But it was pure chance, because I didn’t know anything about it, I hadn’t learned about it. At first, I didn’t understand what had happened, but it was only afterwards that I made the connection; I thought I’d made a mistake, but then I analyzed my mistake: there’s carbon at that temperature and it changes copper. I realized that copper is very sensitive, even at low temperatures.
Soliflore, cristallisation, Copper red, Matthieu Liévois
Following this accidental discovery, how did you pursue your search of color?
I tried to reduce at higher temperatures, but reducing at higher temperatures made the crystals disappear, they became transparent and it didn’t work.
So I continued to smoke-fire, and the pieces came out with a background that could be pink with red crystals, or the background could be gray; it could also be green because I think that in the background of glazes, there’s less salt, there was more oxide. So it must have been at that point. Then I started incorporating other oxides into this copper-based glaze, including antimony. And the antimony changed the copper entirely, and it wasn’t red or green, but yellow, I had copper yellows on a grey background….
At that time, I did a lot of research, but I didn’t touch the firings any more, I had set my firing with these levels. I went back to all my recipes and added ingredients. It became my hobbyhorse.
Soliflore, Red copper and cobalt, Matthieu Liévois
Have you seen the gradual emergence of resources or other research into this complex technique?
Other potters started looking. Later, thanks to the Internet, we were able to exchange information and access articles. Then books were published…
Now, if someone wants to make crystalline glazes, in 3 minutes on the Internet they can find a recipe… that works! Before, it wasn’t possible.
Why do you use an electric oven these days?
Right now, I’d say that 98% of potters who make crystalline glazes use electric kilns. They also use mass colorants quite easily, perhaps.
Potters who crystallize copper reds, like me, use 2 kilns. They first fire the crystals in an electric kiln, then put the pieces back in the kiln, raise the temperature to 800°C for the 3rd firing and then carry out a reduction, which is what I do. This reduction can be carried out with a forced-air kiln, but also in a gazette (a sealed box, a small compartment in the kiln that isolates the piece): the piece is put back in a gazette in the kiln with fuel and raised to 800°C; the gazette is sealed tightly. The fuel flames at first, consumes all the oxygen, and all that’s left is carbon. In fact, this is the raku phenomenon. That’s what you do when you smoke a raku. In fact, you could use a raku kiln for smokestacking.
Tall soliflore, Red Copper and Cobalt, Matthieu Liévois
Crystallization is more than just a technique; it has become your artistic signature. What are you trying to convey through your crystallized pieces?
I’ve made crystalline glazes my trademark. It’s always been a passion. It was with crystallization that I made my name, that I first became known. When people talked about me, they thought of crystallization.
I had a few exhibitions, in Montmorency, near Paris. I did one in Saint-Jean-La-Poterie, in the south of France. I’ve done major shows like the Tupiniers du vieux Lyon and Aubagne. I’ve done Saint-Leu-la-Forêt.
But my biggest market was Diessen in Germany. There was another potter doing crystalline glazes, a Dutchman, but he didn’t use the same techniques.
For my part, I was in a permanent state of research. Crystallization for crystallization’s sake is fine, but I wanted to make something artistic out of it, something that tells a story. It’s a bit like potters who will make a very beautiful glaze, but if they don’t tell something, the glaze is cold. For me, there has to be an effect, a story, a landscape, so that everyone can see different things. What’s more, as I live by the sea, I like the idea of the seabed, where there are extraordinary things, but I also like forests… all nature in the end!
It’s true that it’s very pleasant to make a nice, round pot, or one with a nice, tight shape, with a beautiful, flawless glaze. But once I’ve made one, two, five, ten… I don’t feel like making any more. But it’s precisely by working with crystallization, by superimposing certain glazes that will prevent crystallization in precise places in the pot, that you get a sense of randomness, and above all surprise, which is what interests me most: surprising myself with each firing. Something that works perfectly, when I do it 50 times, by the 51st time I don’t even want to untwist it. Sometimes, I’m disappointed because I think I’ve understood something and then in fact I’ve understood nothing: what I was doing doesn’t work anymore, I don’t know why; and sometimes I do something at random, without realizing it, and it changes everything. That’s the challenge that interests me.
How easy is it to introduce your students to this crystallization technique? How do they react to this challenge?
Well, it’s quite surprising: people either love crystalline glazes or they don’t. There’s no middle ground. When I offer training courses, I’m quite surprised to find that those on crystallization fill up less quickly. Whereas the more classic glazes fill up very quickly. Do people think it’s too complicated? That it’s too demanding? Do they think it’s mainly for the experienced, those who already know? But it’s actually quite exhilarating when you get going. I’ve made it my brand image, but not the only one. It’s not all you want to do. If I’d confined myself to crystallization, I’d have ended up getting tired.
The proof is that you’re getting into earthenware, and that’s quite unexpected on your part…
That’s a real challenge. You think it’s simple, but it’s not easy at all when you want to make utilitarian pieces, because often the glaze cracks and the pots are not watertight. Earthenware glazes are made from frits, like crystalline glazes, and from this a new idea was born… to make crystal glazes by replacing the frit with earthenware glazes, but at high temperature.
Yellow earthenware glaze fired at 980°C. In the following photos, this glaze has replaced frit in several crystallization recipes and has been tested on porcelain and various stoneware:
Blue-gray earthenware glaze fired at 980°C. In the following photos, this glaze has replaced frit in several crystallization recipes and has been tested on porcelain and various stoneware:
It’s interesting to use earthenware glazes not so much for the earthenware itself. In a ceramics catalog, you have a fairly limited choice of frits. On the other hand, we have 500 earthenware glazes, so there’s a huge range of possibilities with earthenware that we don’t have with frits, and that’s what interests me in the end: the challenge of finding something. And above all, it’s completely unexpected once again.
Here, I’ve found a grey-white earthenware glaze on, test tiles and I think it’s zirconium-based. And when I introduce this grey-white earthenware glaze into a crystalline glazes recipe, I get some really beautiful white crystals. But in the past, every time I put zirconium in my glazes, I didn’t get any crystals! As earthenware melts very well at 980°C and I fire at 300°C higher for crystallization, the fact that it’s more melting makes it possible to obtain crystals.
Brown earthenware glaze fired at 980°C. In the following photos, this glaze has replaced frit in several crystallization recipes and has been tested on porcelain and various stoneware:
I also have a 100-kilo stock of earthenware glaze, which turns a not-very-beautiful brown, but in crystalline glazes glazes, it gives me something splendid, on stoneware and not on porcelain! These are crystals, which aren’t very big, but they leave different colors.
This quest for crystallization is never-ending, and the introduction of earthenware glazes once again opens a huge door for me.
White earthenware glaze at 980°C. In the following photos, this glaze has replaced frit in several crystallization recipes and has been tested on porcelain and various stoneware:
I’m going to start buying earthenware glazes or making them myself! Because with a frit, you can also make earthenware glazes, which is why it’s a good idea to have bought a tiny test kiln like the one we acquired at the beginning of the school year. But all this is going to take me a long time, and I think my retirement will be quite busy!
Pavot Vase, Matthieu Liévois
Many thanks to Matthieu Liévois for this extremely rich testimonial.
We remind you of our previous article on the practical application of glaze crystallization.
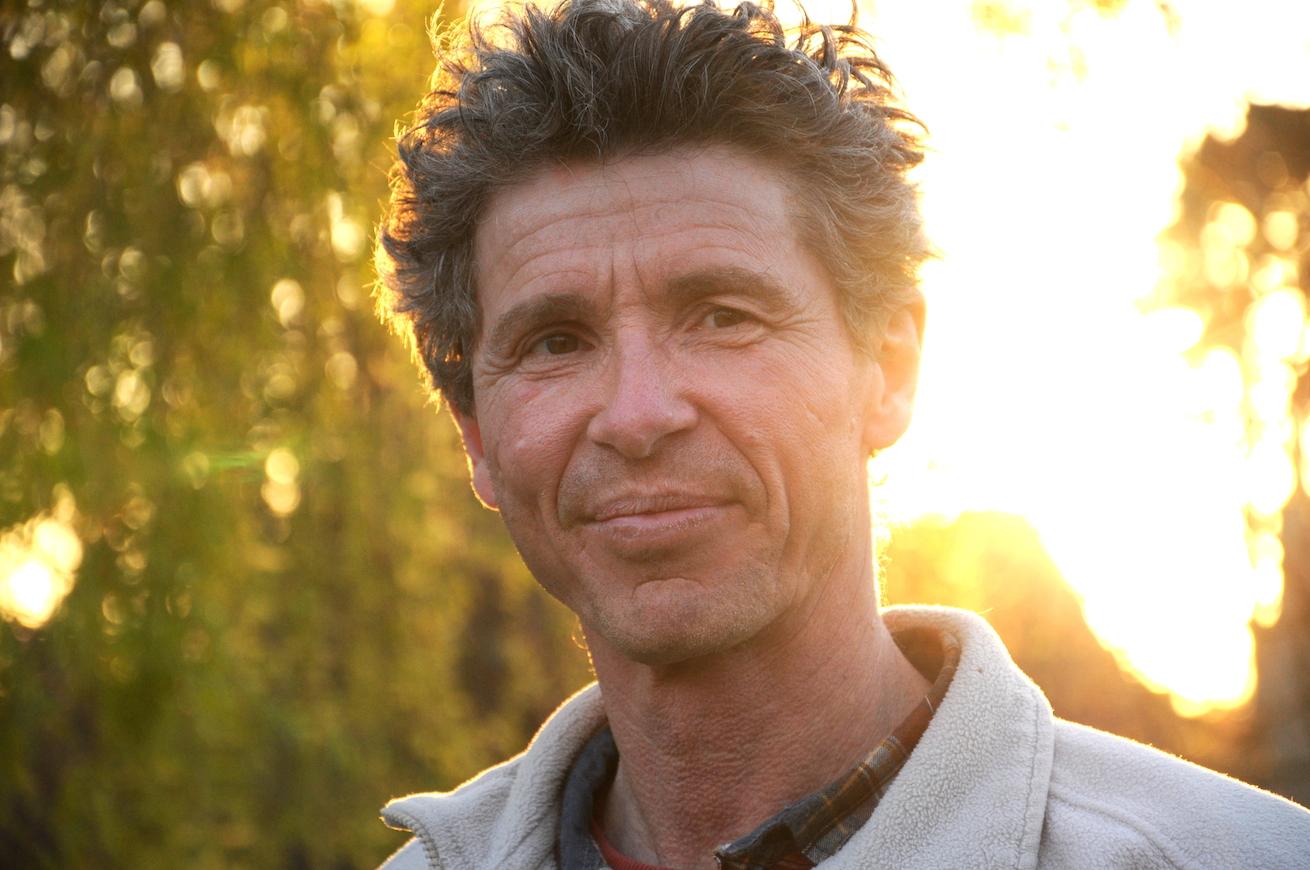
Resource centre
animated by Matthieu Liévois,
potter-ceramist for over 40 years and founder of the Creamik School
Find all the courses
Keywords
Don’t miss any more news from the Créamik school!