When to buy a kiln
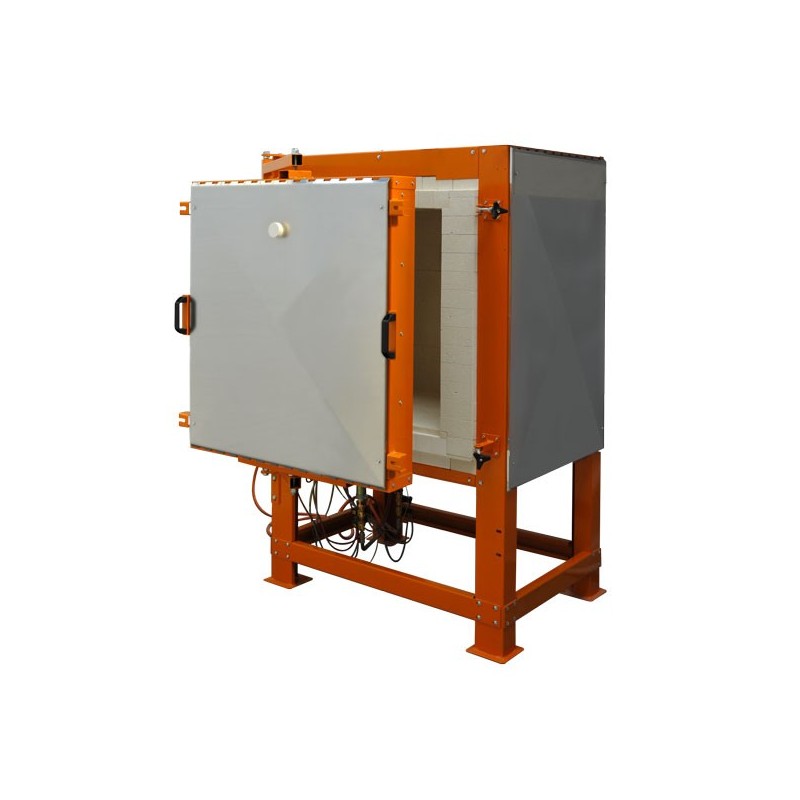
It is not necessary to be an experienced ceramicist to realize that the choice of a kiln will demand all our attention.
To choose a kiln, you must know what type of pots you want to make, because this will determine which clay or glaze you will use and therefore at which temperature you need to fire. As the work of the potter changes with experience and becomes more defined, one should not make too hasty a choice either: it may limit future development in your work. The kiln is an important and expensive purchase which will not be replaced often. Here are some tips to help you choose the right one.
Is firing your pottery in a professional potter’s kiln a good option?
It may seem reassuring to start by firing your pottery in a friend’s kiln. However, moving the pieces to another workshop involves a lot of handling with all the inevitable breakages (packaging, boxing, transport of very fragile pieces not yet fired, etc.), not to mention the time lost, the fuel . . . Firing in a different kiln from the one you are used to can lead your glazes to perform differently. You may have to adapt to this new kiln as your glazes may look very different.
Once you set up your studio, the purchase of a kiln should be done right at the beginning. The kiln’s dimensions will be a major element in how you organize your studio space.
It is a little different for the amateur potter, starting their adventure in pottery. Firing at a professional’s studio will then be a good idea. It helps them to progress and learn.
Keep in mind that it is not always practical for a professional potter to fire other people’s pottery. Time spent firing someone else’s work may be to the detriment of his/her own.
In addition, the professional potter takes a real risk firing other people’s work. Many amateurs may not know that some of their pots will not be compatible with all firings: earthenware (1150°C (2102°F)) cannot be fired in a kiln set to fire at a stoneware temperature (1300°C (2372°F)). If fired at a temperature that is too high, the clay will not be overfired, it will simply melt on the kiln shelves and damage it beyond repair.
Same with glazes: you may have chosen a clay compatible with a certain kiln, but the glaze might be too runny in another kiln. Then, both kiln shelves and pot may be lost. Glaze can drip onto the shelves, the burners or the bottom of the kiln: all this has unfortunately happened to many potters! A damaged Kiln stops the entire production process.
Before firing in someone else’s kiln, discuss what materials you are using, and make sure you both understand the likely gas or electricity cost, as well as the number of pots and their sizes. You can then agree on a fair price for the firing.
Once a satisfactory arrangement has been made the cooperation should go smoothly, and everyone will come out as a winner.
If I buy a kiln, what should I pay attention to?
Of kilns available on the market (new or second-hand), electric kilns have a significant advantage: their size. There are small electric kilns that can easily be installed in an existing garage for instance. You will just have to think about the power supply and possibly switch to a three-phase circuit. However, electric kilns will only fire in oxidation which can quickly become frustrating as reduction firing can produce more varied and beautiful glazes.
Gas Kilns are a wise choice since they allow both oxidation and reduction firing. However, installation is more complicated than it is for an electric kiln.
The size of a high temperature gas kiln is quite substantial. This example is the smallest of the French-made Bretagne kilns, with a capacity of 170 litres. Its external measurements are 1.75 m height, 1.03 m width and 0.85 m depth. You would need to make sure there is space above for the chimney and sufficient space around to open the door wide, load your pots . . .
You will also need to connect a gas supply – for a small 170 L kiln, you can choose 4 propane bottles of 35 kg.
The room must be well-ventilated, to avoid any problem linked to the carbon monoxide the kiln will release. The best solution is to install your kiln in a garden shed and not in your studio.
Considerations like this show that the choice of a kiln is not simple, and that careful thought is needed before buying one.
But firing is the most critical moment, technically and creatively, in making pottery. Not having your own kiln will considerably slow down your production and challenge your motivation in certain situations.
A kiln is central to setting up a studio, and you need to budget for one as soon as you can, planning and organising the physical space so that you have easy access to it.
Can you install your kiln in a shed or in your garden?
The kiln should be as close as possible to your studio to avoid breaking pots when transporting them to be fired. Having a kiln far away from your studio can be problematic.
Often, when loading the kiln, a little glaze can fall off a pot: you will need to quickly run back to the studio to fix it. When it rains, you will not be able to load the kiln . . . etc.
Finally, if the kiln is too far away, you waste a lot of time walking to and fro to monitor the firing, especially when you want to check the gas exhaust in reduction. You need to be working while the kiln is on for those 6 hours, and not spending most of your time in your garden checking your firing!
So, which pottery kiln to choose?
Obviously, spending something like 10,000 to 15,000 euros to set up your studio may seem like a big investment (the main expense will be the kiln). Compared with other professional activities, it is actually not such a big investment, and you should not be afraid to take this risk. Do not fall for a “cheap” or “cheaper” kiln: some small low-cost kilns are generally for earthenware and will not exceed 1150°C (2102°F) temperature. You are likely to regret your purchase once you deepen your knowledge and start making your own glazes and use high firing clay such as stoneware or porcelain. Let’s not forget that less is sometimes more.
A small gas kiln, going to a high temperature, connected to gas bottles, could be a good compromise. Make sure you install it in a large enough space though because, if sales go well and production increases, you will want a larger one. The advantage of the small gas kiln is that it is highly sought after on the second-hand market, it will resell very well . . . allowing you to buy a larger kiln . . .
Installation of 4 propane bottles supplying a 170 litre Bretagne Kiln.
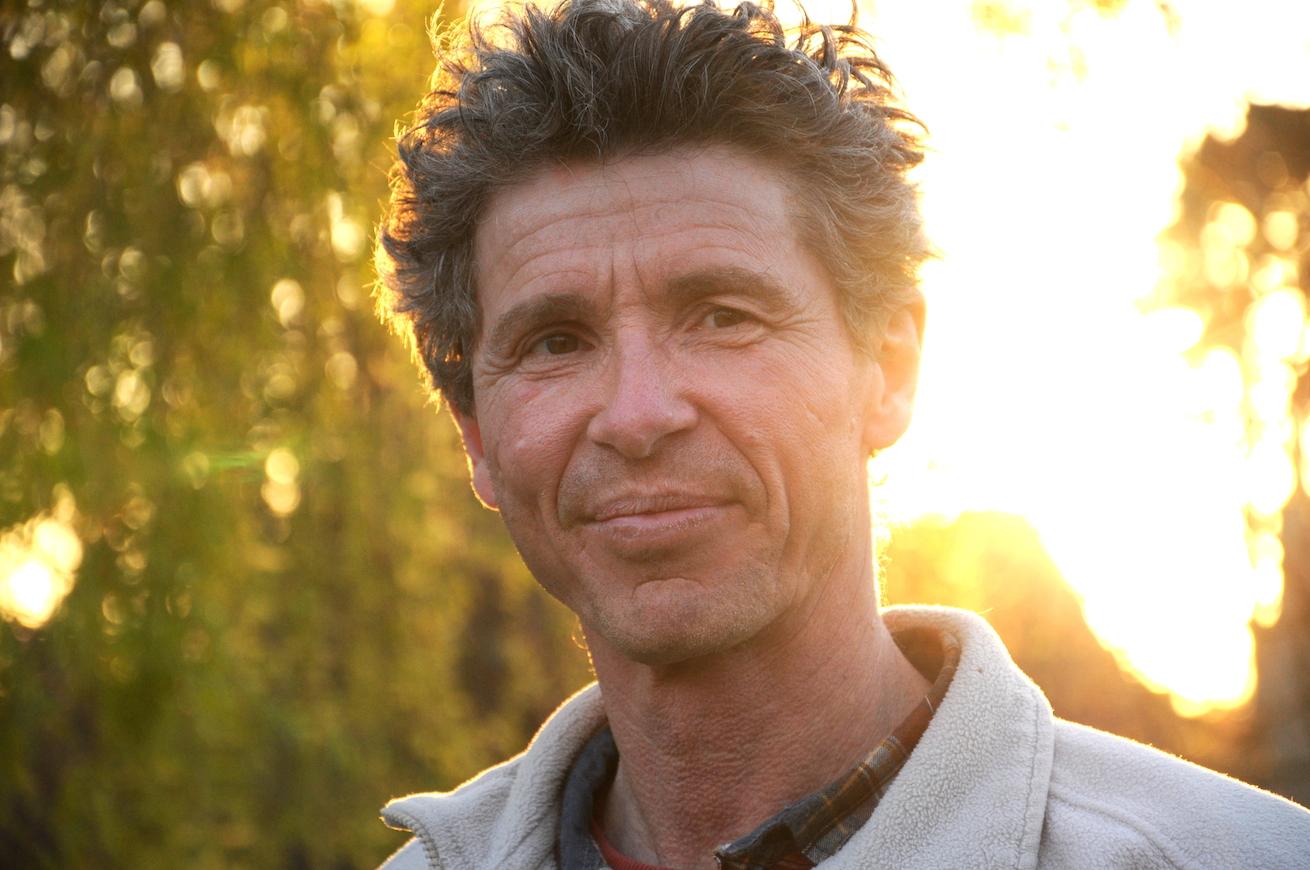
Resource centre
animated by Matthieu Liévois,
potter-ceramist for over 40 years and founder of the Creamik School
Find all the courses
Keywords
Don’t miss any more news from the Créamik school!