How to calculate the cost of firing?
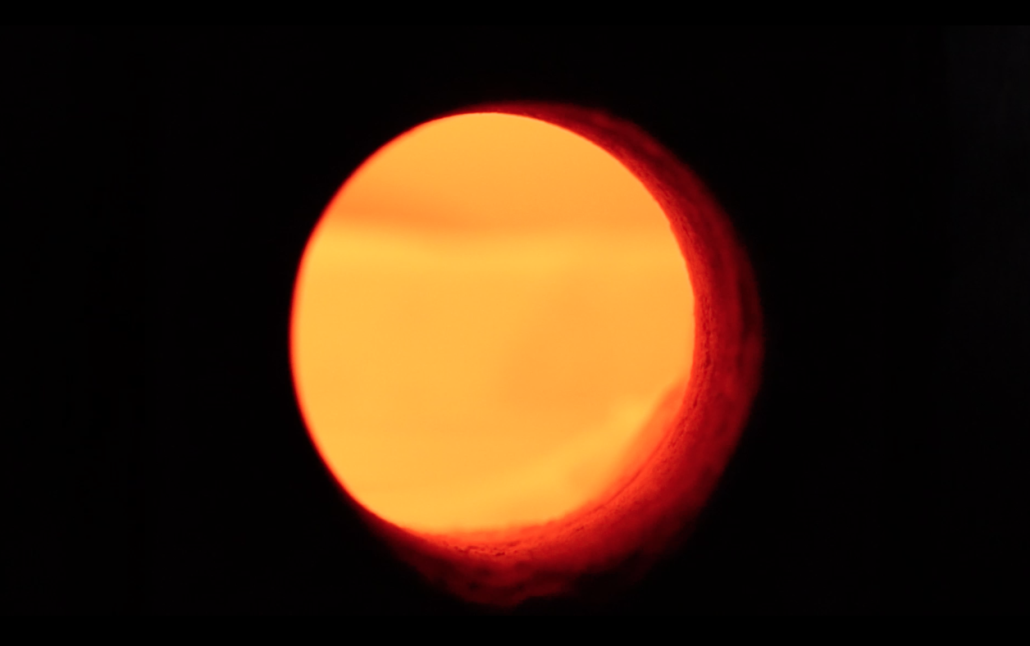
Summary
The electric kiln: simplicity and convenience
• Make the best use of your working time
• The gas kiln: control and flexibility
• Understanding Insulation in a Kiln
The wood kiln: tradition and lower cost
A few practical tips before choosing your kiln
Tip on how to pay for the fuel
How to calculate the cost of firing?
If the answer was simple, the question would not come up so often. In this article, we will calculate the price of different firings, taking into account different kiln specifications. Knowing the exact cost of a firing will help you choose the kiln you buy. It also allows you to price the products you sell accurately. There is a paradox in ceramics: the difference between the clay price and the kiln price. You start with very cheap materials, but the cost of a kiln and its fuel is quite another matter. Clay will never be expensive; this permits you to hone your skills, especially if you are good at reclaiming material that has been worked but does not end up in the finished pot. On the other hand, the kiln does not leave much room for mistakes.
The electric kiln: simplicity and convenience
Volume
Electric kilns are a recent development in ceramics and have certainly made the profession more widely democratic. There is a wide choice of brand, size and prices Electric kilns are the least expensive, and there are a range of models to cater for amateurs and professionals. Whether you use an amateur electric kiln or a professional electric kiln, its atmosphere will always be oxidized. To be precise, the atmosphere is “neutral”. The electric kiln heats up, and that’s it. This does not stop you from making beautiful glazes, but the choice is more limited compared to a gas or a wood kiln. All brands combined, the capacity of a kiln ranges from 20 L to 2000 L, or even more. You need to decide which size best suits your output. Assess each kiln carefully, as the capacity may vary in between different manufacturers.
We will classify electric kilns into 4 categories:
- The smallest kilns, (15 L) are perfectly suited for beginners, for those who want to produce small quantities, or as test tile kilns.
- Medium-sized kilns (50 to 200 L) are for semi-pros or professionals with a large output. Bigger pieces of different sizes can be fired.
- Large-size kilns: (200-500L) are suitable for professionals with an extensive output.
- Industrial kilns: (500 L and more) are for in large-scale production, such as ceramic factories.
Power
The power of a potter’s kiln depends on its volume, its insulation, its temperature range and the speed at which it will reach and maintain high temperatures. You will need to check with your electricity provider to ensure that the power needed for your kiln is compatible with your supply. Energy suppliers offer between 3 kWh and 36 kWh. What to choose, Les furets, or Kelwatt? Whatever your provider, if you have a kiln with high energy consumption, or are in any doubt, you must take advice from a qualified electrician and if necessary check with your supplier. An electric kiln goes on and off during the full cycle, but when it reaches high temperatures, your supply must sustain this energy-intensive usage, especially if other electrical appliances are connected (in particular the water heater). You also need to make best use of off-peak pricing. An unexpected stoppage of the kiln caused by an electrical failure is a huge risk to your production. A change in your contract may increase your tariff, and change your terms and conditions. You need to make sure your energy supplier will not require a second meter for your ceramic activity. Finally, depending on the power of your kiln, it may be necessary to switch from single-phase ) to three-phase. ( A three-phase supply can accommodate higher loads, and deliver power at a steadier, more consistent rate. Generally, single-phase current is capable of handling devices up to approximately 7-9 kWh. Above this, a three-phase installation is recommended.
Here is a summary of the power ratings of kilns, using our previous classification:
1. The smallest kilns: from 3 kWh
2. Medium-sized kilns: 5 to 10 kWh
3. Large kilns: 10 to 20 kWh
4. Industrial kilns: 20 kWh and more.
Again, these are a ballpark figures, with variations depending on the specific model and its energy efficiency. It should be noted that the number of kWh indicated is not the consumption per hour, but the total power of the kiln. To obtain the actual consumption, the length of time the kiln is operating must be taken into account.
Make the best use of your working time
It’s worth noting, when calculating the cost of a firing, that an electric kiln does not require supervision: the controller manages it. As a precaution, we check that everything is going well, especially when we are still unfamiliar with the kiln but, as a rule, once the controller is programmed, the kiln runs by itself. When connecting the kiln, a conventional wall socket will not be used: the electrician will install a dedicated socket. You can also choose a direct connection to the box, in which case there is no longer a socket. The power will then be turned off directly at the circuit breaker. The risk of accidents will be reduced.
• Cost of firing
We are now going to estimate the cost of an 8 hour firing at 1300°C /2372°F for different kilns. The costs are calculated for peak hours, off-peak hours, for electricity supplied in France by EDF at a commercial rate in force in June 2023:
Type of kiln kiln |
Volume | Power | Cost (normal hours) |
Cost off peak hours |
Cost commercial rate |
The smallest kilns | 15 L + | starting at 3 kWh | 3 kWh * 8 h * 0,2228 €/kWh = 5,34 € 5,34 € |
3 kWh * 8 h * 0,1615 €/kWh = 3,88 € 3,88 € |
3 kWh * 8 h * 0,1752 €/kWh = 4,21 € |
Medium size kilns | 50 to 200 L | 5 to 10 kWh | 10 kWh * 8 h * 0,2228 €/kWh = 17,82 € | 10 kWh * 8 h * 0,1615 €/kWh = 12,92 € | 10 kWh * 8 h * 0,1752 €/kWh = 14,02 € |
Big size kilns | 200 to 500 L | 10 to 20 kWh | 20 kWh * 8 h * 0,2228 €/kWh = 35,65 € | 20 kWh * 8 h * 0,1615 €/kWh = 25,84 € | 20 kWh * 8 h * 0,1752 €/kWh = 28,03 € |
Industrial kilns | 500 L + | 20 kWh + | 40 kWh * 8 h * 0,2228 €/kWh = 71,30 € | 40 kWh * 8 h * 0,1615 €/kWh = 51,68 € | 40 kWh * 8 h * 0,1752 €/kWh = 56,06 € |
This table is based on the assumption that the kiln operates at full capacity during the entire firing process, which in reality is not the case. So, it gives an approximate estimate of the maximum cost of a firing.
The gas kiln: control and flexibility
Gas kilns offer great flexibility in terms of control. The management of the atmosphere –-which can be oxidizing, neutral and reducing – allows unique results. However, this flexibility comes at a cost. Gas kilns are generally more expensive to install and operate. They are clearly for professional or semi-professional ceramicists. It is labour intensive to operate a gas kiln. Even if the kiln is equipped with a controller, someone needs to manage how and when the gas comes in. In forced-air kilns, the potter also manages the introduction of the air into the kiln. This constant presence needs to be included in the cost.
• Understanding Insulation in a Kiln
Gas kilns can be insulated with refractory bricks but also with refractory ceramic fibre (RCF). Refractory ceramic fibre heats up quickly and is cheap and efficient – the fibre does not need to be heated. RCF allows firing to 1300°C/2372°F in 6 hours, with very good results. Firing in a brick kiln is three times as expensive as firing in a refractory fibre kiln, because you must heat the bricks. While firing in a 300 L kiln insulated with refractory fibre will cost 10 to 12 euros, it will cost 45 to 50 euros in a kiln insulated with refractory bricks. Cooling in a brick kiln will take longer, which can be very favourable for the glazes. But it also means you will leave your pots an extra day in the kiln and won’t be able to use your kiln as often. Finally, it’s easier to buy a brick kiln that a fibre kiln. Top loading gas kilns start at 45 L. For front loading gas kilns, the range starts around 150 L.
Cost of firing
The details here apply to France, but should give an idea of how to calculate costs elsewhere. Unlike natural gas or electricity, the price of propane (LPG) is very loosely regulated. It’s important to compare prices and to negotiate. If your kiln offers the possibility of using 13 or 35 kg propane bottles, go ahead and install a tank. A tank has constraints and costs, but is very easy and comfortable to use. Here is an average of the costs of propane per ton, in an above ground tank, and in a buried tank. The calculations were made from an average of different suppliers’ prices quoted online in June 2023:
Medium size above ground tank | Medium size in a buried tank | |
Price of propane gas by the ton | 1500 € | 1500 € |
Annual cost | 3300 € | 3500 € |
Cost over 3 years | 10000 € | 10600 € |
Cost of annual subscription | 200 € | 225 € |
End of contract cost | 400 € | 1000 € |
How Creamik does it
Let’s take the concrete example of the Bretagne gas kiln we use at Créamik. It is a 300 L kiln, with 2 burners, insulated with refractory fibre. For gas, we have a communal subscription with a group of potters which allows us to pay 1.12 € per kg, or 1123 € per ton of gas. For 9 hours firing to 1280°C/2336°F (in reduction), the kiln consumes 16.5 kg of gas. The cost of firing is €18.48 including tax. We have an underground tank, with a subscription of €120 per year for maintenance, which is carried out systematically every year by “Primagaz”, a famous gas company in France.
The following is an example of the creation of a collective in France. We are sharing it here, to give you ideas of what can happen. Check in the country you live in if similar organisations have been set up, and if not, why not start one yourself, with fellow potters?
The French collective creation:
Following a huge gas cost increase in 2000, a group of potters noticed the sharp difference between one gas provider and another and decided to form an association called Collectif National des Céramistes. They have now followed the lead of an association of potters in Aveyron called Teranga, and have negotiated with Primagaz for the best price. To join “Collectif National des Céramistes” you need to fill in a form as a professional potter. A membership card will be sent to you as well as to Primagaz. There is a one off 10 euros membership payment. Once you are a member, if you contact a local Primagaz provider, you will benefit from the negotiated rate. The prices are for 500 kg or 1 tonne tanks, but you can also find interesting discounts on smaller bottles.
The wood kiln: tradition and lower cost
Wood-fired kilns are the traditional method of firing pots. They are often large and require constant monitoring. Despite this, they can be an economical option in rural areas where wood is abundant and inexpensive. This article is not focusing on wood kilns. However, the intensity and length of the firing, the smell, the noise and all the atmosphere that wood creates makes wood firing a fascinating experience . . . And while waiting for the firing to finish, why not watch “Grand feu en Puisaye, an adventure in pottery country” by Jacques Tréfouël and Daniel Hénard, or “All Fire All Sandstone” by Petra van Heesbeen?
A few practical tips before choosing your kiln
To find out when to buy your kiln, check our article.
Once you have chosen between gas and electric, choose the right size for your needs. Firing, in fact, should neither be a handicap nor a constraint, there are already enough of these before the firing stage! Make sure your bank loan is not too heavy, the kiln not too big or too small, and easy to operate. Avoid second hand kilns (even donated ones), they may not be expensive, but are often energy-intensive and too heavy, and they may be beyond repair, or spare parts may be unobtainable . . .
Favour a well-known manufacturer with good customer service, over a private dealer.
But do not forget that you do not necessarily need a gas kiln to make beautiful glazes. Ash glazes can be fired in an electric kiln and give magnificent results. In addition, using an electric kiln is quite simple, while it takes 5 to 10 firings before you get to know your gas kiln. So what are the weak points of an electric kiln? They are more fragile and require more maintenance than gas kilns. You need to change the elements every 50-60 firings (between 400 and 600 euros, depending on the kiln’s dimensions). Electric kilns are less and less expensive but also have a shorter lifespan (from 300 – 400 firings only). In comparison, a gas kiln’s lifespan is 10 times longer. The question to ask: is it better to have a cheap kiln which will need to be replaced every three years or an expensive one you keep for 10-15 years?
Up your game with experience
In conclusion, when starting your business, start either with a small second-hand electric kiln (no more than 10 years old), or a new one at a reasonable price. Aim for a capacity of 110-160 L, and power not more than 12 kWh. When you can generate a sufficient and lasting profit, invest in a more expensive kiln, the depreciation in value of which may be written off against tax. You may buy a small Raku or a wood-fired kiln at a low price, but in terms of glazes, you will be quickly limited. Note: a person with the right skills can turn a homemade wood-fired kiln into a gas kiln (€1000 for the bricks and €300 per burner), but it will be a much less efficient kiln than those made by specialist manufacturers.
Installation of a kiln
Finding the right place (both location and ventilation) for a kiln requires some thought. These aspects can have an impact on the safety and efficiency of the firing, and therefore indirectly on its cost. A good studio layout can help reduce operating costs and improve the firing process.
Tip for financing fuel consumption
With a little bit of planning, firing does not cost as much as we imagine. If the loading is optimized, the cost of fuel per item is very low. Even so, for a gas kiln, the bill for filling the gas tank remains “the painful one” . . . So how can you plan to meet this cost? In loading the kiln, there are always places in which we can slide small pieces, flat or not very high, especially under objects that have an open shape (bowls, salad bowls, ball vases, etc). Including very small items, for instance those made with stamps or in moulds, can fill the smallest of spaces and reduces the cost. It is best to make moulds (especially for small objects) when it will not impede your main work: at the end of the day or between other activities. These small pieces, which require little time to make, and which have little glaze on them can sell for 3 to 5 euros. The profits from these can help finance the fuel. By helping with the bill in this way, we may find greater peace of mind . . .
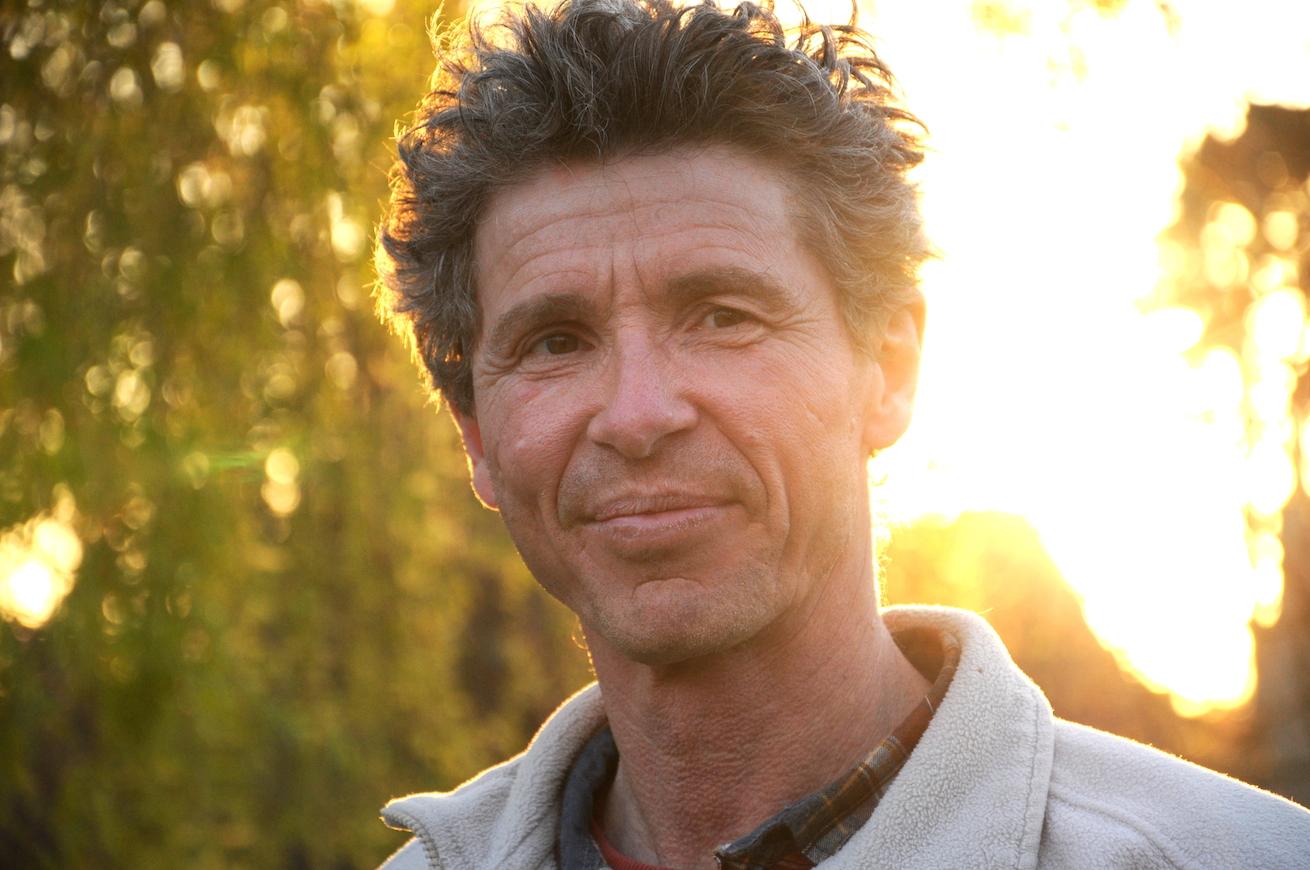
Resource centre
animated by Matthieu Liévois,
potter-ceramist for over 40 years and founder of the Creamik School
Find all the courses
Keywords
Don’t miss any more news from the Créamik school!